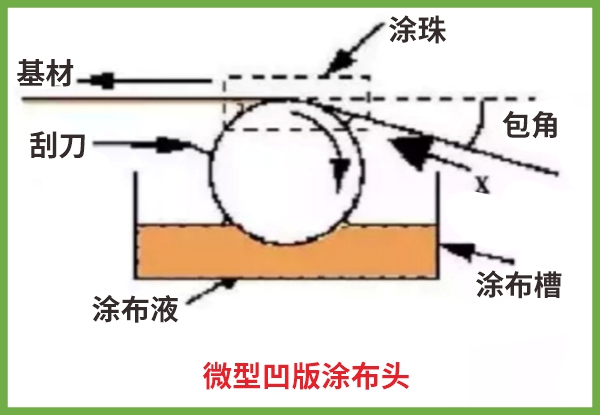
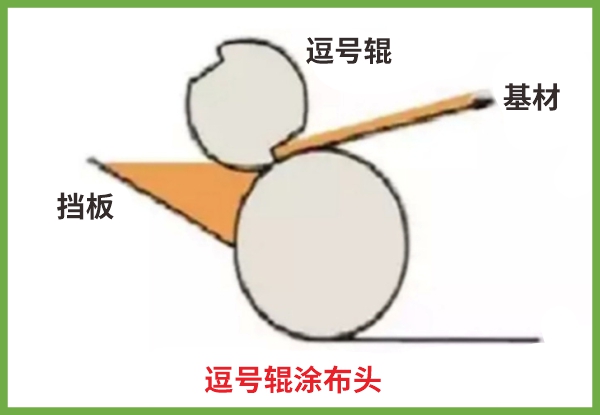
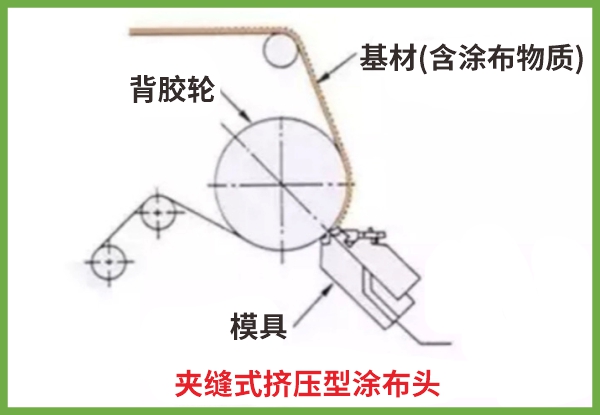
Silicone solid state compression molding process:
The precision coating molding process is divided into micro-gravure coating, knife coating, and slit extrusion coating according to the coating head. The micro-gravure coating roller is an anilox roller, and the diameter is generally between Φ20mm-Φ50mm, so it is called micro-gravure coating. It is a reverse contact coating method, that is, the rotation direction of the micro-coating roller and the feeding direction of the material film On the contrary, the material film is not pressed against the coating roller by the pressing roller. The doctor blade coating roller is a comma doctor blade. The characteristic of the comma roller coating is the combination of blade blade and roller blade, which has less influence on the glue thickness than glue, and the coating thickness is easy to adjust. It can coat high viscosity glue. When the width is large, Can be adjusted horizontally. Slit extrusion coating is a common high-precision coating method. The coating glue is pressed from the memory through the supply pipe to the nozzle, and the glue is ejected from the nozzle to transfer to the coated substrate.
Product specifications:
Product effective width 1070mm, thickness 19um-250um
Product Features:
· The product has high coating precision, stable peeling force, and a wide range of applications
· Silicone coating has the characteristics of high and low temperature resistance, acid resistance, and no glue residue after tearing off
· Polyurethane coating has good fit and stable adhesion and easy to tear off
· With high cleanliness and high light transmittance, no glue residue or ghost after use
Main product categories, names, characteristics and MSK raw materials
Silicone semi-finished materials SiParts
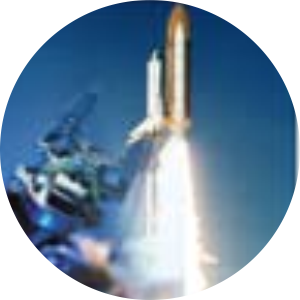
Able to meet future needs
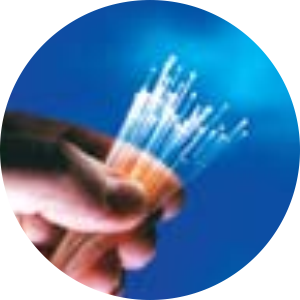
Suitable for various industrial fields and multiple purposes.
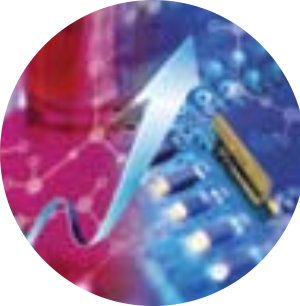
By combining organic and inorganic materials, Improve the chemical and physical properties of materials.
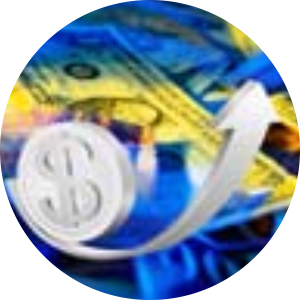
Has a stable structure
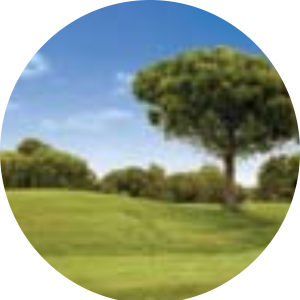